Polymer changes temperature, shape when charged, moving to where the heat needs to be.
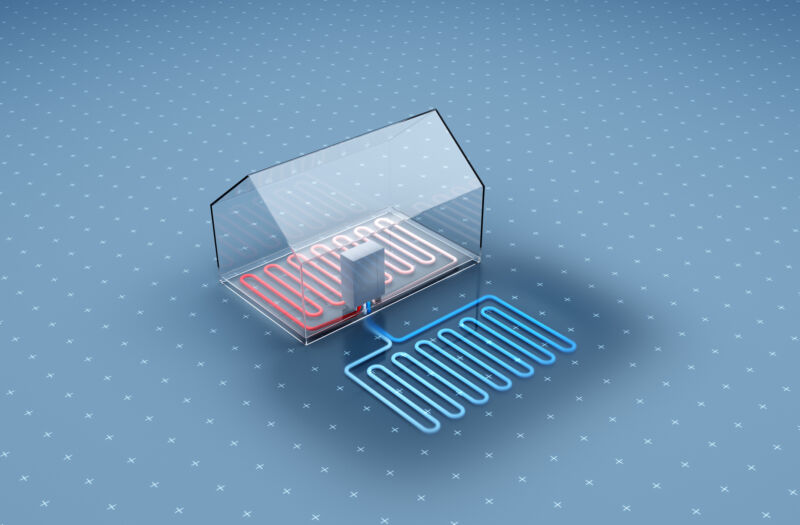
Heat pumps are the most energy-efficient way of controlling indoor temperature. By moving heat between locations, they avoid the inefficiencies of generating heat in the first place. But that doesn’t mean they can’t be made more efficient.
Most current heat pumps rely on materials that exhibit large changes in temperature in response to changing pressures, but the energy required to pressurize them gets lost when they’re cycled back to a low-pressure state, absorbing heat from their surroundings. That has gotten people interested in electrocaloric devices, where changes in temperature are driven by storing charges in a material. Since it essentially acts as a big capacitor, much of the electrical energy involved can be pulled back out as the system cycles.
But capacitors aren’t especially mobile, so electrocaloric systems tended to use fluids to move heat into and out of the capacitor as it cycles. Now, however, researchers have developed an electrocaloric system that moves itself between hot and cold environments, radically simplifying the system and eliminating some of the energy required for it to operate. They even demonstrate it effectively cooling a computer chip.
Electrocalorics and heat pumps
Late last year, we covered a paper that described a demonstration electrocaloric system. It operated pretty simply: Pumping electrons into a capacitor caused a phase transition in its internal electronic structure. While this phase transition doesn’t involve melting or freezing, it is associated with a major change in the capacitor’s heat content.
But, on its own, that won’t operate as a heat pump. While it will happily either heat or cool its immediate environment (depending on whether it’s being charged or discharged), that doesn’t help you transfer heat between environments. To heat or cool an environment, you need to move heat energy out of or into the capacitor. The team that developed this device did so by simply pumping water.
So, to act as a cooling device, the electrocaloric capacitor would first heat up water that would then be pumped to where it could radiate that heat away to the environment. New water would then be pumped in, which the capacitor would cool during discharge. That cool water would then be pumped to where it could absorb heat from the area that was meant to be cooled.
It definitely works, but there is an energy cost associated with doing that pumping. The new work, done by researchers at the Shanghai Jiao Tong University, gets rid of the need for any pumping. Instead, the capacitor itself moves between the heat source and heat sink. And it does so when powered by the same thing that triggers the temperature change: being charged or discharged.
The work relies on a polymer called poly(vinylidene fluoride-trifluoroethylene-chlorofluoroethylene), a name so complex that even the abbreviation is excessively long (we’ll just refer to “the polymer”). It’s a known electrocaloric material, but variants of the polymer with a different chemical bonding structure have a different response to picking up charges: They change shape.
So, the researchers spent a fair bit of time testing chemical reactions that produced polymers with different frequencies of double bonds, attempting to maximize both effects: electrocaloric temperature changes and charge-driven shape changes. This was undoubtedly a significant amount of work, but it takes up roughly three sentences in the paper. In any case, with the chemistry sorted out, they could make a single polymer that had strong temperature and shape responses.
ARS VIDEO
What Happens to the Developers When AI Can Code? | Ars Frontiers
Putting it to work
Turning that into a heat pump is remarkably simple. Let’s say you have a surface you want to cool down. You simply arrange the polymer so that its shape after discharge (which cools the polymer) leaves it physically touching that surface. Then, when you add charge to it, it will both change shape to move away from the surface and start heating up. If you arrange things so that it comes in contact with a second surface at this point—say a heat sink or a large reservoir of water—it will dump its heat into that and return to ambient temperature and be ready to start the cycle all over again.
In other words, the polymer would move itself between warmer and cooler environments and do so in response to the same process that causes it to change temperature. If you can get the geometry to work out, then it’s a single-material heat pump that is powered by charging and discharging a capacitor—with most of the electrons used to do the charging still available to power something else when the cycle is complete. It can also work for heating or cooling, depending on how you configure the system.
And it works. The researchers configured a setup where the polymer acted as a cooling system for a computer chip that would normally be operating at 60° C. With the electrocaloric system operating, the chip’s temperature dropped by 18° C. By contrast, a cooling fan only dropped the chip’s temperature by 7° C.Advertisement
The material is also remarkably durable, with no drop in performance seen after 70,000 cycles. They also showed it was possible to build an array of as many as 260 individual polymer devices to cool larger objects, which was able to transfer heat with an efficiency of about a third of the maximum allowed by the second law of thermodynamics.
Capacitors with lots of potential
The researchers found that the key determinant of performance was the interaction between the surface of the polymer and the material it was transferring heat to or from. Optimizing this thermal contact, they write, will be “essential to further enhance the performance of the self-oscillating electrocaloric device.”
While individual pieces of polymer may not be able to drive huge temperature differences (although a 17° C difference is not at all bad), it’s also easy to see how you can build a device with lots of these pieces of polymer in series, with pairs of polymers flipping between different sides of a single metal plate. Depending on how many layers of devices you make, you could control the size of the overall temperature gradient.
This may not completely eliminate the need for some sort of working fluid to transfer heat over longer distances. Things like water heaters in the basement or computer chips are typically in environments where a large source of ambient temperatures can be some distance away. But the nature of that fluid really doesn’t matter—it could easily be water. So this development has the potential of freeing us from the chemicals that are currently used in most heat pumps, which are typically potent greenhouse gases.
Nature, 2024. DOI: 10.1038/s41586-024-07375-3 (About DOIs).